The Future of Maintenance in Cement. Man-Free, Wear-Free, Self-Repairing?
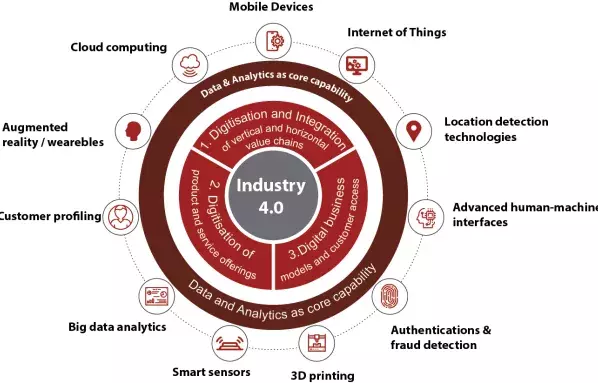
Cement is used to make concrete, the most consumed manufactured substance on the planet. However, the cement sector is the third-largest industrial energy consumer, comprising 7% of the global industrial energy use and represents 7% of the total of all CO2 emitted globally.
Cement Plant/Industry Trends for the Future
From the above trends and CO2 targets it is clear that cement plants of the future will be focused on CO2 reduction, increased use of alternative fuels and improving plant energy efficiency (electrical and thermal).
In addition, to support these initiatives there will also be strong operational financial demands such as:
- Maximum plant availability: No unplanned downtime or waiting for spare parts delivery
- Longer operational campaigns and shorter outages
- Maximum plant operating performance: as designed by plant OEMs
- Less plant staff. Multi-tasking, younger-less experienced. Training will be key
- Maintaining benchmark operational standards in new, remote locations
- Lower spare parts stock
Many believe that Industry 4.0 will not readily apply to cement, but the first steps were already taken many years ago with Condition Monitoring of critical motors/drives and deployment of gas sensors throughout the plant to balance combustion and emissions. With the continuous consolidation in the cement industry, benchmarking a plant’s operational performance and efficiency is important for cement groups. This data can also be used to improve equipment design by the OEM. An ideal system to collect data using current IoT technologies is illustrated in attached image.
Whilst vibration monitoring on drives have a long history, Wear Sensors are a new development. One system being developed involves measurement directly of: type of wear, wear rate and profile changes over time and these could be linked to operating condition data. The Wear Sensor technology had a big potential leap with the commercialisation of 3D cameras in smart phones for profile mapping. Increasing grinding processes efficiency is also critical.
New process modelling and simulation software can determine an optimal grinding component design. Real world data is being added to these models that include casting and surface defects which can also predict and avoid operational failure.
The elements of wear monitoring, new wear and corrosion resistant materials, advanced wear modelling and new maintenance technologies will play a crucial role in achieving the future goals of the cement industry, and could wholeheartedly embrace the Maintenance 4.0 philosophy.